Mounting of IKO CRWG series and CRWG…H series
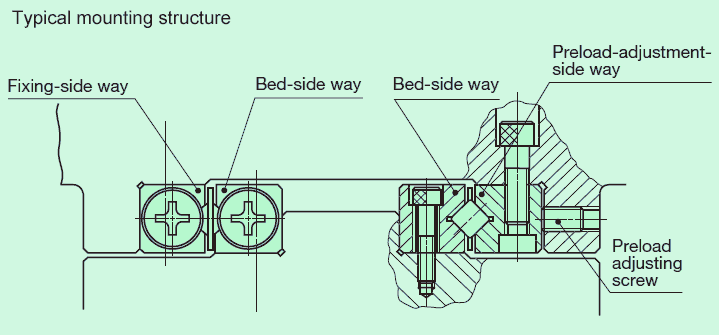
For mounting at this point, generally follow the procedure below.
1, Preparation for mounting
IKO crossed roller way guides are packed by set (4 ways and 2 pairs of roller cages). Be careful not to mix with other sets.
Remove end screws and end stopper, clean up each part with clean wash fluid and then apply rust prevention and lubrication oil.
2, Cleanup of mounting surface
Remove burrs and blemishes on the machine mounting surface with an oil-stone, etc. Be careful about corner groove on the mounting surface, too.
Wipe off dust and dirt with clean cloth and apply rust prevention and lubrication oil lightly.
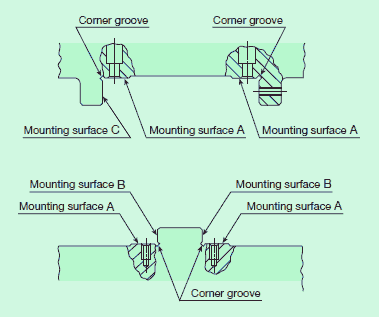
3, Mounting of bed-side way
Properly align the way with mounting surface and temporarily tighten fixing screws evenly to the tightening torque.
While making the way sticking to B surface tight, fully tighten the screws to the specified torque.
When high running accuracy is required, fully and evenly tighten them to the specified torque while checking the parallelism of the raceway along the full length of the way.
Typical tightening torque for fixing screw refer to Tightening torque for fixing screw
4, Operation of table and bed
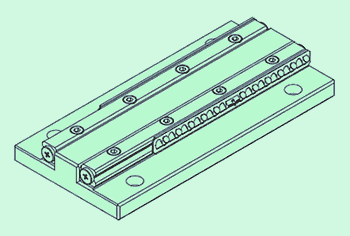
Position the roller cages at the stroke end positions of the bed-side way.
Mate the pinion gear at the center of the cage and the rack of the way.
At this point, be careful not to deform the cage.
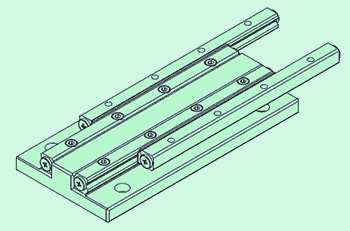
Position the table-side way in the stroke end position.
Mate the pinion gear at the center of the cage and the rack of the table-side way.
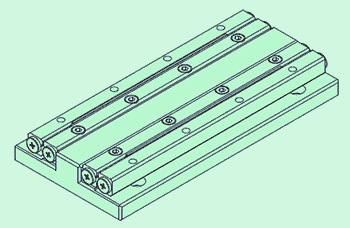
Position the table-side way approximately in the stroke center position.
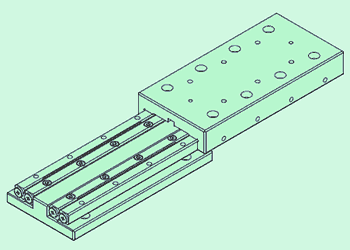
Position the table while holding the way to prevent it from moving.
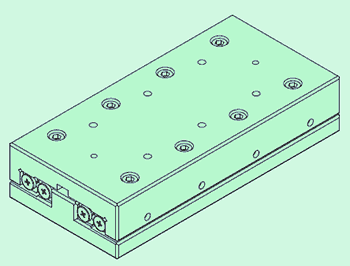
Temporarily tighten the table fixing screws.
Fully stroke the table softly and check that it is within the stroke range used and cylindrical rollers on both ends of the cage do not contact with end screws of the way. If they make contact, take the procedure again.
5, Preload adjustment
Preload adjustment is performed with fixing screws of the table-side way tightened temporarily.
Preload adjustment is started from the preload adjusting screw at the center of way length and then both ends in turn.
While measuring the clearance on the table sides, tighten the preload adjusting screws subsequently until deflection of the dial gauge stops. Measure the tightening torque for preload adjusting screws at this point.
When adjusting preload adjusting screw near either end, stroke the table softly and check that the cylindrical roller is on the preload adjusting screw section.
After the above procedure, the clearance becomes zero or in slight preload state, but preload is still not adjusted evenly. With the same procedure again, re-adjust all the preload adjusting screws evenly to the torque previously measured.
6, Full tightening of preload-adjustment-side way
Fixing screws are lightly tightened to even torque. As with preload adjusting screws, temporarily fix them to torque similar to the specified torque in turn from the way center to both ends.
When tightening fixing screws near either end, stroke the table softly and check that the cylindrical roller is on fixing screw section.
Finally with the same procedure, fully tighten all the fixing screws evenly to the specified torque.
7, Check after assembly
Fully stroke the table softly and check that running is smooth without abnormal noise.
Measure the table upper and side surfaces with dial gauge or the like and check the running accuracy.
Mounting of IKO standard type CRW series
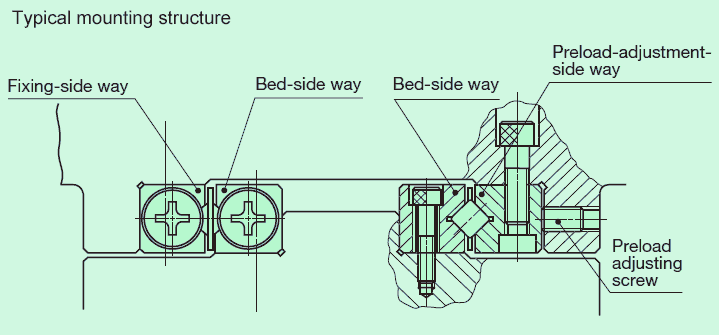
For mounting at this point, generally follow the procedure below.
1, Preparation for mounting
Products are packed by set (4 ways and 2 pairs of roller cages). Be careful not to mix with other sets.
Remove end screws and end stopper, clean up each part with clean wash fluid and then apply rust prevention and lubrication oil.
2, Cleanup of mounting surface
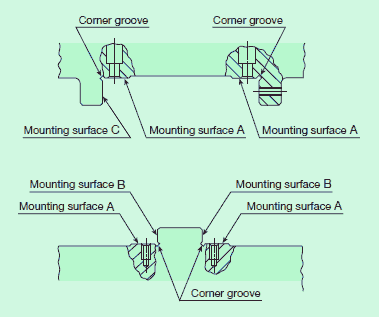
Remove burrs and blemishes on the machine mounting surface with an oil-stone, etc. Be careful about corner groove on the mounting surface, too.
Wipe off dust and dirt with clean cloth and apply rust prevention and lubrication oil lightly.
3, Mounting of bed-side way
Properly align the way with mounting surface and temporarily tighten fixing screws evenly to the tightening torque.
While making the way sticking to B surface tight, fully tighten the screws to the specified torque.
When high running accuracy is required, fully and evenly tighten them to the specified torque while checking the parallelism of the raceway along the full length of the way.
Typical tightening torque for fixing screw refer to Tightening torque for fixing screw
4, Mounting of table-side way
Properly align the fixing-side way with mounting surface and temporarily tighten fixing screws evenly to the tightening torque.
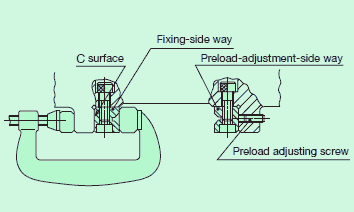
While making the fixing-side way sticking to C surface tight, fully tighten the screws to the specified torque.
Set back the preload adjusting screws in advance, make the preload-adjusting-side way sticking to the mounting surface, and then temporarily tighten fixing screws lightly to the even torque.
5, Operation of table and bed
Make alignment of the position in height and cross direction so that the roller cage can be inserted between the table-side way and bed-side way.
Carefully insert the roller cage and assembly it at approximate center of the way length. At this point, be careful not to deform the cage.
Mount end screws and end stopper of each way.
Push the entire table against the preload adjusting screws and tighten the preload adjusting screws to make temporary adjustment until the clearance between ways becomes zero.
Fully stroke the table softly and correct the roller cage position to the center.
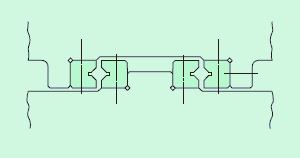
6, Preload adjustment
Preload adjustment is performed with fixing screws of the preload-adjusting-side way tightened temporarily.
Preload adjustment is started from the preload adjusting screw at the center of way length and then both ends in turn.
While measuring the clearance on the table sides, tighten the preload adjusting screws subsequently until deflection of the dial gauge stops. Measure the tightening torque for preload adjusting screws at this point.
When adjusting preload adjusting screw near either end, stroke the table softly and check that the cylindrical roller is on the preload adjusting screw section.
After the above procedure, the clearance becomes zero or in slight preload state, but preload is still not adjusted evenly. With the same procedure again, re-adjust all the preload adjusting screws evenly to the torque previously measured.
7, Full tightening of preload-adjustment-side way
Fixing screws are lightly tightened to even torque. As with preload adjusting screws, temporarily fix them to torque similar to the specified torque in turn from the way center to both ends.
When tightening fixing screws near either end, stroke the table softly and check that the cylindrical roller is on fixing screw section.
Finally with the same procedure, fully tighten all the fixing screws evenly to the specified torque.
8, Check after assembly
Fully stroke the table softly and check that running is smooth without abnormal noise.
Measure the table upper and side surfaces with dial gauge or the like and check the running accuracy.
Mounting of IKO moudule type CRWM series
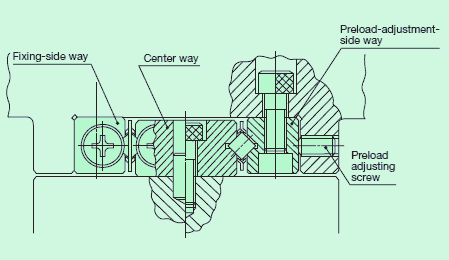
For mounting at this point, generally follow the procedure below.
1, Preparation for mounting
Crossed Roller Way is packed by set (1 center way, 2 ways and 2 pairs of roller cages). Be careful not to mix with other sets.
Remove end screws and end stopper, clean up each part with clean wash fluid and then apply rust prevention and lubrication oil.
2, Cleanup of mounting surface
Remove burrs and blemishes on the machine mounting surface with an oil-stone, etc. Be careful about corner groove on the mounting surface, too.
Wipe off dust and dirt with clean cloth and apply rust prevention and lubrication oil lightly.
3, Mounting of center way
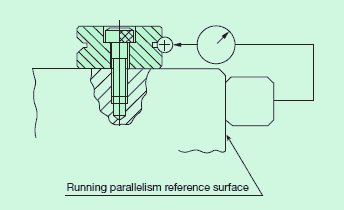
Mounting accuracy check for center way
Roughly align the center way to the mounting surface and lightly fix it with fixing screws.
While measuring mounting parallelism of the center way and raceway to the reference surface of running parallelism for position correction, temporarily tighten the fixing screws to the even tightening torque.
Evenly tighten all the fixing screws to the specified tightening torque.
4, Processing of dowel pin hole
When dowel pins are used, machine holes on the bed in alignment with dowel pin holes near either end of the center way.
Dowel pin hole of the center way is finished for H7. Finish bed holes in the same way.
Diameter and its allowance of dowel pin hole of the center way vary depending on the dimension table.
Eliminate cutting chips and clean up again as necessary. When machines for mounting of the center way are large, clean them up with the center way removed and then reassemble.
Load the dowel pins and check the parallelism of the reference surface of the running parallelism and the raceway of the center way again.
5, Mounting of table-side way
Follow the mounting of standard type CRW series.
6, Operation of table and bed
Follow the mounting of standard type CRW series.
7, Preload adjustment
Follow the mounting of standard type CRW series.
8, Full tightening of preload-adjustment-side way
Follow the mounting of standard type CRW series.
9, Check after assembly
Follow the mounting of standard type CRW series.
Mating marks module type CRW series
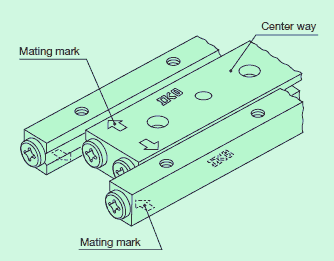
CRWM has mating marks to ensure the best running accuracy af ter mount ing based on the paral lel ism measurement result of reference mounting surface and raceway. When assembling the ways, align the mating marks of ways with the same end side as indicated in picture above.